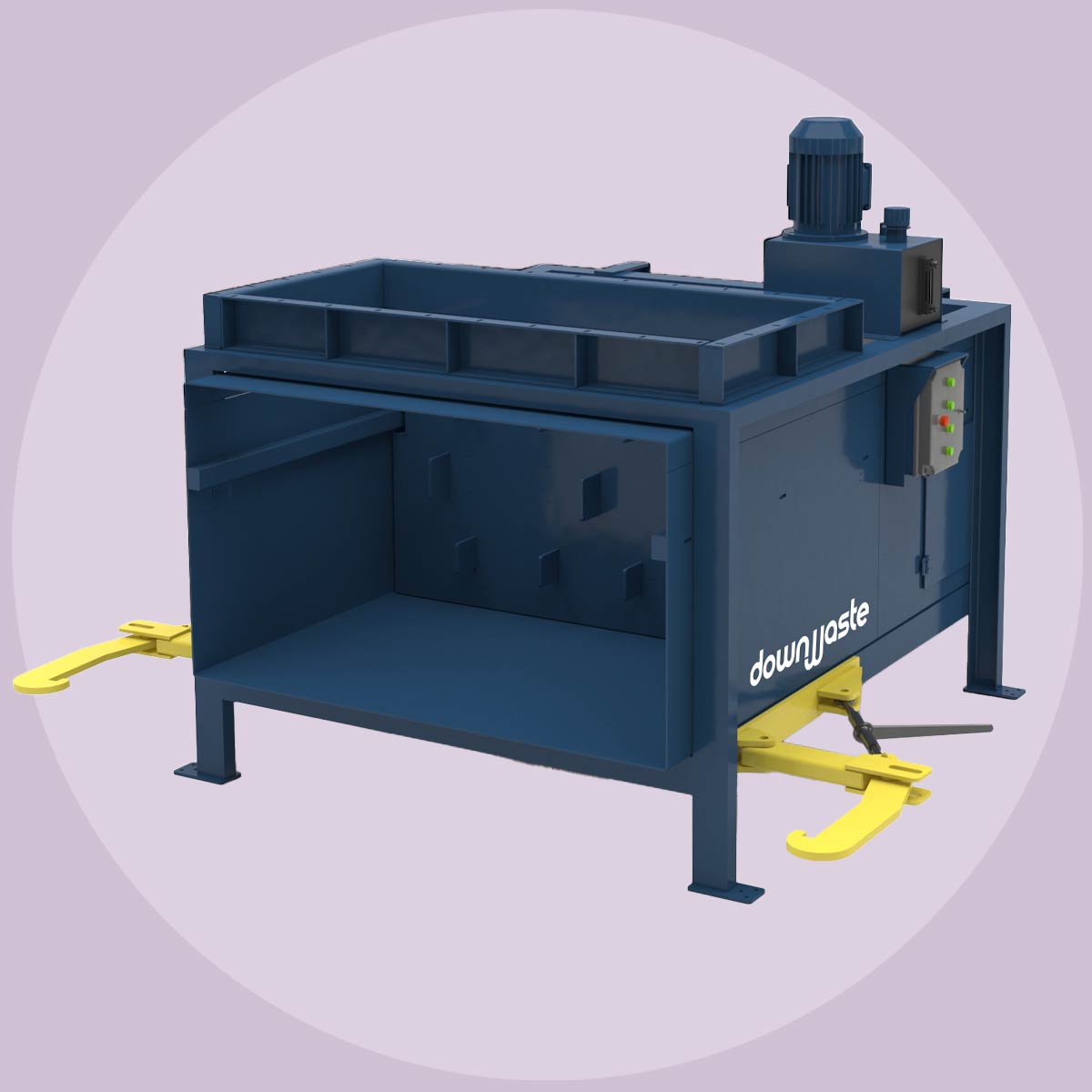
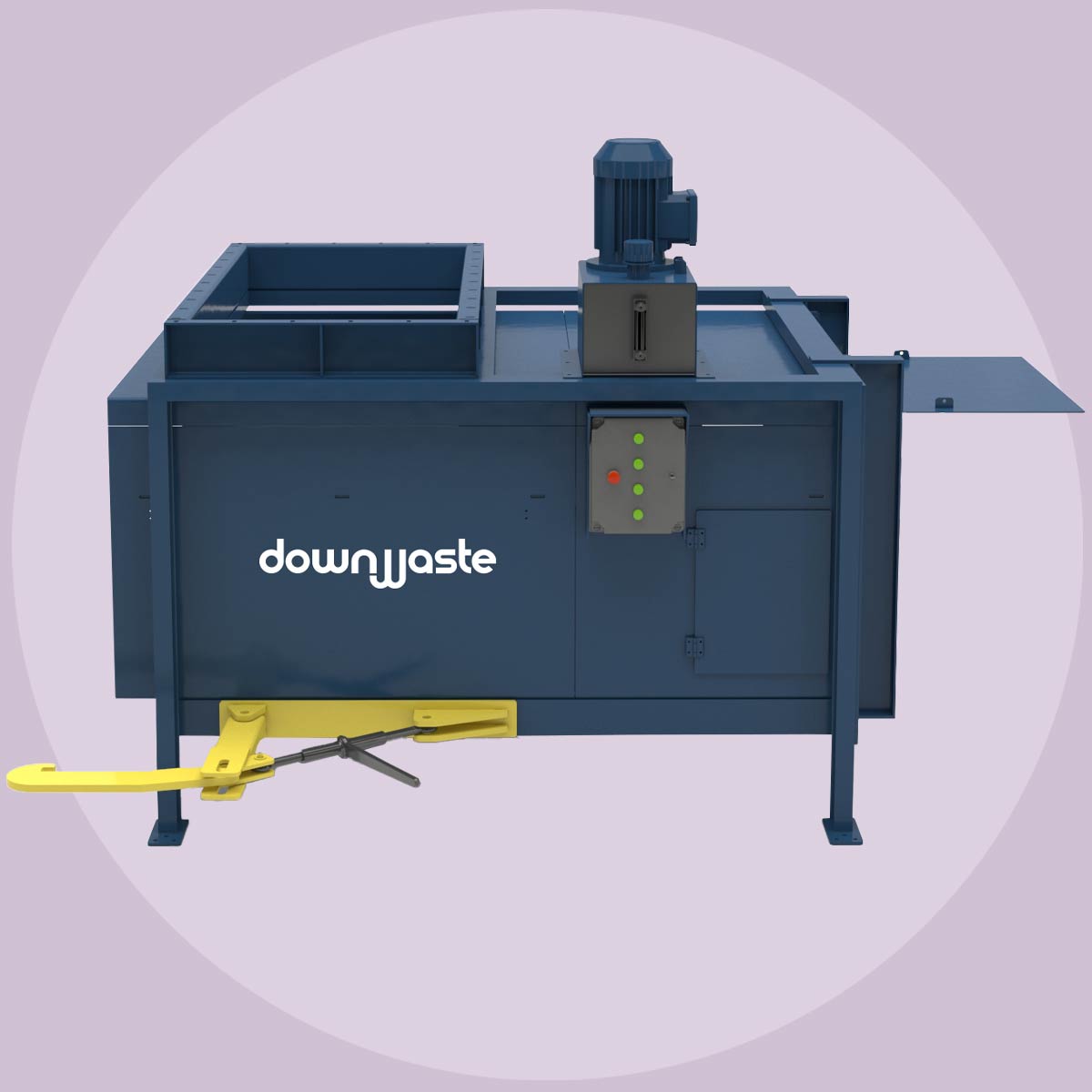
STATIC COMPACTORS
Downwaste static hydraulic waste compactors offer significant cost savings by maximising the volume reduction of your waste and recyclables, leading to lower disposal expenses. The machine’s operation is straightforward and safe, making it easy for your personnel to use and ensuring a smooth workflow. With a substantial fill opening our static waste compactors are unmatched in the market, allowing for efficient handling of large volumes of waste.